Maximize Product Life and Minimize Maintenance
Purpose-Built Tension Solutions from Concept to Production
Applied Fiber creates and manufactures synthetic cable assemblies that are purpose built around our client’s requirements. From standard rope and cable products terminated with standard fittings to complex tension systems that benefit from fully optimized and integrated components, we work with each client to explore their design options and develop the most optimal tension solution.
Engineering And Product Development
Applied Fiber provides full engineering and product development services to take products from concept to production. This would include services such as conceptual modeling for fit and weight checks, stress modeling, system design consultation, component engineering and optimization, prototype development, lab and field testing, etc.
Our industry leading experience and expertise helps provide our clients with the right tension solution quickly and efficiently. Our application-focused product development process begins by understanding important design factors such as:
- System Design and Function Requirements
- Typical Loading Conditions
- Working Load and Breaking Requirements
- Tensile and Bend Fatigue Requirements
- Elongation / Stiffness Requirements
- Weight Requirements
- Dimensional Constraints
- Interacting System Hardware
- Connection Possibilities
- Environmental Conditions
- Cosmetic Fit/Finish Requirements
- Special Production Requirements
- Special Performance Requirements
- Safe and Reliable Use Considerations
- Regulatory Considerations
- Cost Requirements
- Service Life
Prototyping
Applied Fiber offers quick turn around on pre-production prototypes for evaluation and testing purposes. Many preliminary assessments can be made using standard Applied Fiber products. Custom prototypes are available; from rapid prototyping for fit checks to short run production units for qualification testing.
Testing And Certification
Applied Fiber provides complete testing services to qualify and produce products around specific performance requirements. Available in house testing services include proof load testing, break load testing, tension fatigue testing, bend fatigue testing, compression testing, environmental testing, cable batch testing, resin testing, and elongation/stiffness testing. We additionally manage qualification programs that include specialized lab testing such as multi-axis shock loading, vibration, UV exposure, salt spray, thermal shock, etc.
As a manufacturer of complete tension assemblies, Applied Fiber utilizes state-of-the-art tensile testing equipment that provides lab precision and traceability in a high speed, production setting. 100% product testing is typically included for critical performance applications and can be certified in accordance with regulatory and client requirements.
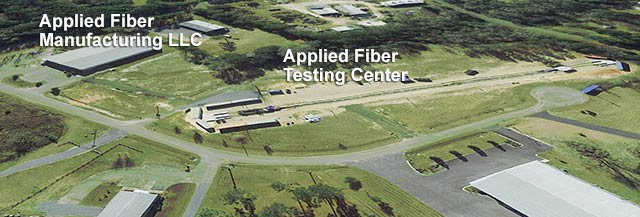
Manufacturing
Manufacturing synthetic fiber rope and cable assemblies is Applied Fiber’s core business. Our experience, technology, capabilities, and quality systems in the field of terminated synthetic fiber assembly production are second to none.
Our processing expertise and technology are focused on consistent delivery of repeatable product that is fit for use in high volume manufactured products and high-risk applications where performance and reliability are critical.
We manufacture purpose-built cable assemblies in diameters ranging from 0.004” (.1 mm) to over 5” (127mm) – from specialty engineered single-use to high volume production.
Our ISO9001 Quality Management System is designed specifically around production of synthetic fiber cable assemblies, with focus on ensuring every important step in the production process has been measured, controlled, and documented appropriately for the application.